Telsa sells defective crap, sticks customers with the bill
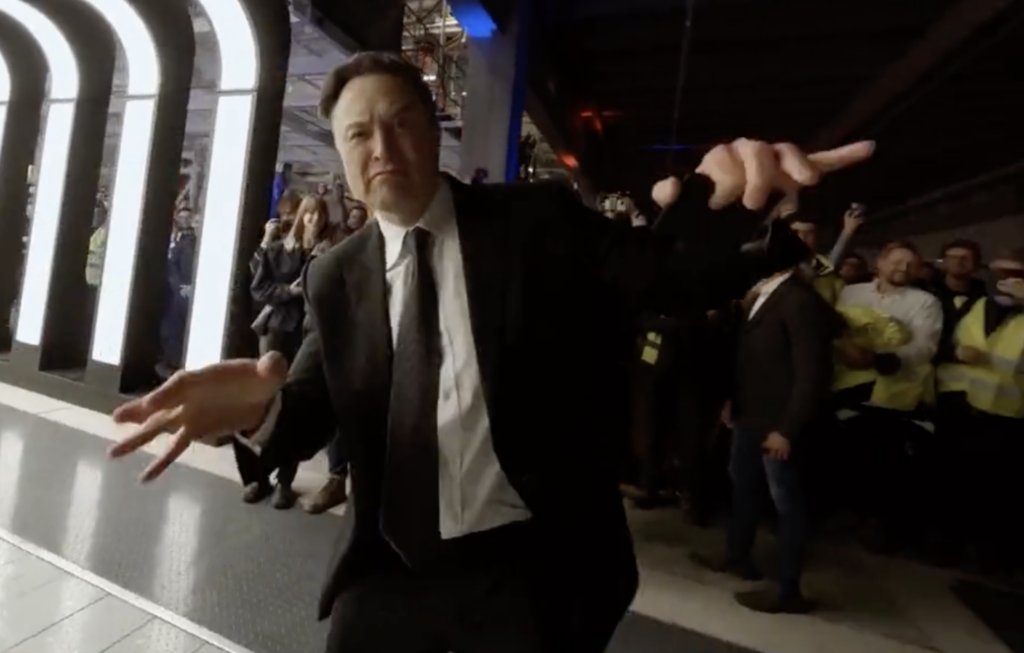
A very thorough investigation with some terrifying results:
Shreyansh Jain was ecstatic in March when he picked up his first electric vehicle, a brand-new 2023 Tesla Model Y. He used a sizable chunk of family savings to buy it with cash.
“We were over the moon!” said Jain, an electronics engineer in Cambridge, England.
His exuberance came to a “grinding halt” one day later, with 115 miles on the odometer, Jain told Reuters. As he drove with his wife and three-year-old daughter, he suddenly lost steering control as he made a slow turn into their neighborhood. The vehicle’s front-right suspension had collapsed, and parts of the car loudly scraped the road as it came to a stop.
“They were absolutely petrified,” Jain said of his wife and daughter. “If we were on a 70-mile-per-hour highway, and this would have happened, that would have been catastrophic.”
The complex repair required nearly 40 hours of labor to rebuild the suspension and replace the steering column, among other fixes, according to a detailed repair estimate. The cost: more than $14,000. Tesla refused to cover the repairs, blaming the accident on “prior” suspension damage.
Jain is one of tens of thousands of Tesla owners who have experienced premature failures of suspension or steering parts, according to a Reuters review of thousands of Tesla documents. The chronic failures, many in relatively new vehicles, date back at least seven years and stretch across Tesla’s model lineup and across the globe, from China to the United States to Europe, according to the records and interviews with more than 20 customers and nine former Tesla managers or service technicians.
Individual suspension or steering issues with Teslas have been discussed online and in news accounts for years. But the documents, which have not been previously reported, offer the most comprehensive view to date into the scope of the problems and how Tesla handled what its engineers have internally called part “flaws” and “failures.” The records and interviews reveal for the first time that the automaker has long known far more about the frequency and extent of the defects than it has disclosed to consumers and safety regulators.
The documents, dated between 2016 and 2022, include repair reports from Tesla service centers globally; analyses and data reviews by engineers on parts with high failure rates; and memos sent to technicians globally, instructing them to tell consumers that broken parts on their cars were not faulty.
In summary, exactly the quality and integrity one would associate with Elon Musk. A lot more damning detail at the link, too — the story is very well done. I would recommend looking into an EV made by an actual auto manufacturer.